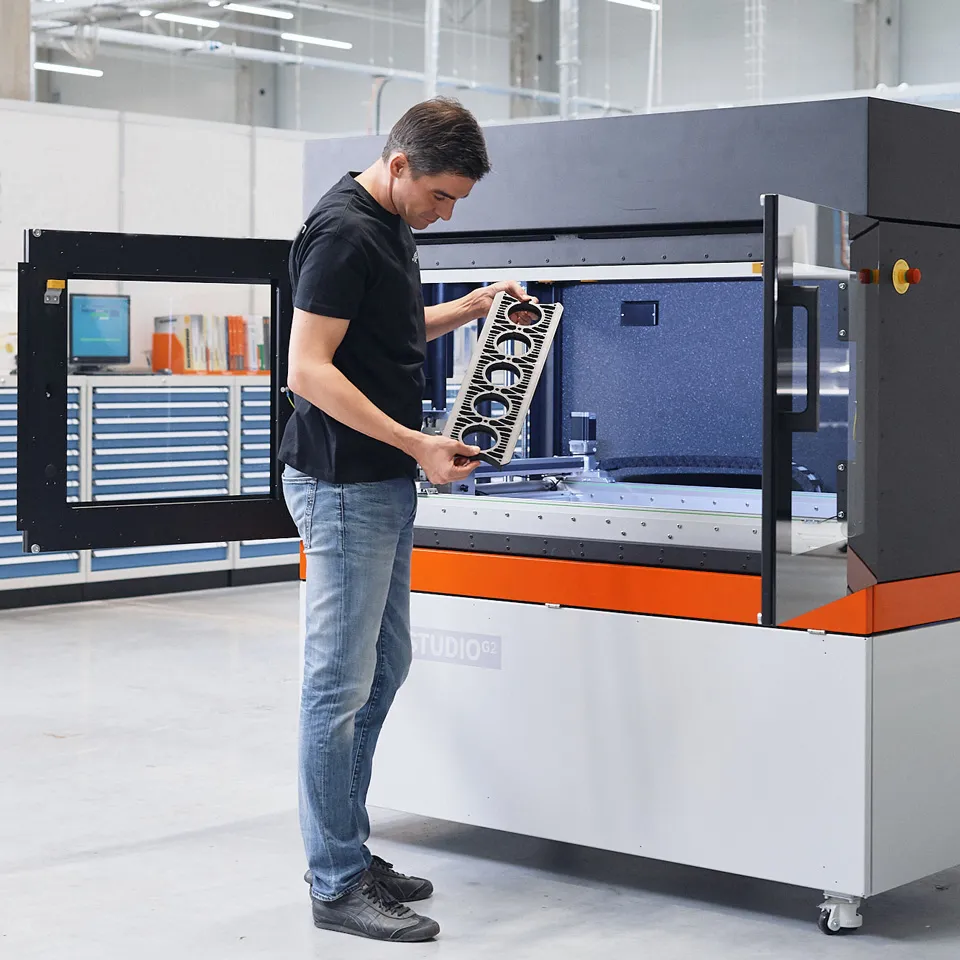
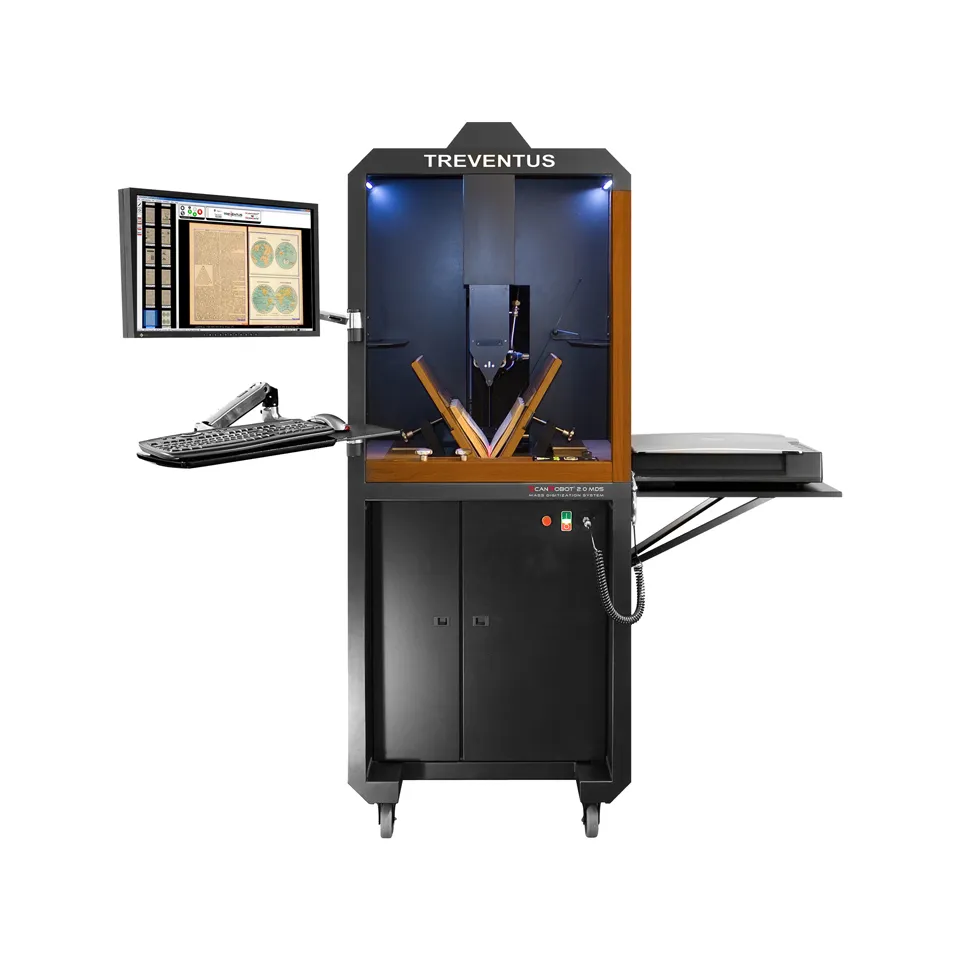
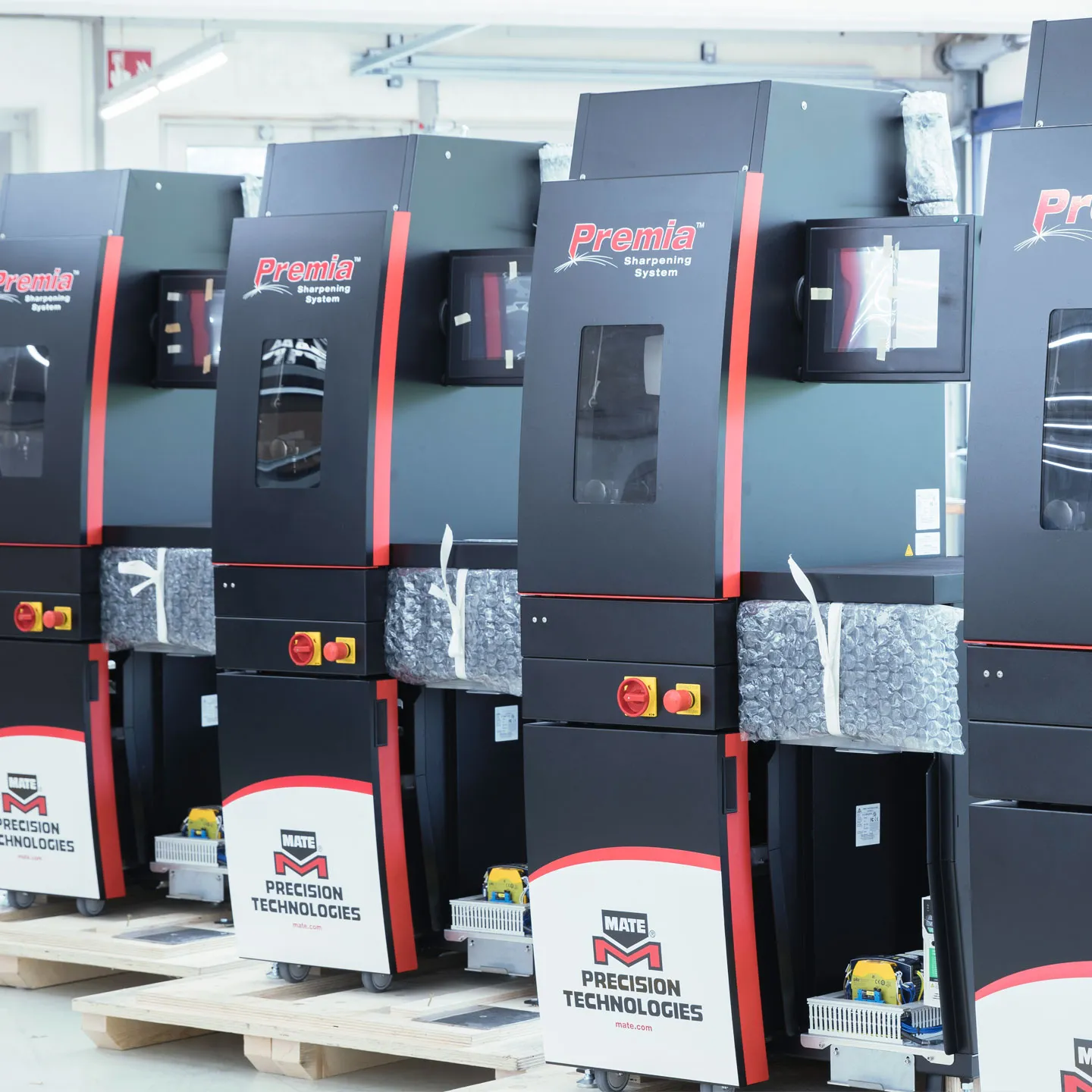
Machine including final inspection
Entire value chain
We have the entire value chain to manufacture all components for your machine ourselves. This results in short distances and optimal quality control.
rassemblement
- Pre-series assembly in Germany
- Economic-scale series assembly in Hungary
Our assembly specialists work strictly according to the assembly instructions and ensure the highest quality workmanship, including acceptance tests. Including cable assembly and control cabinet construction
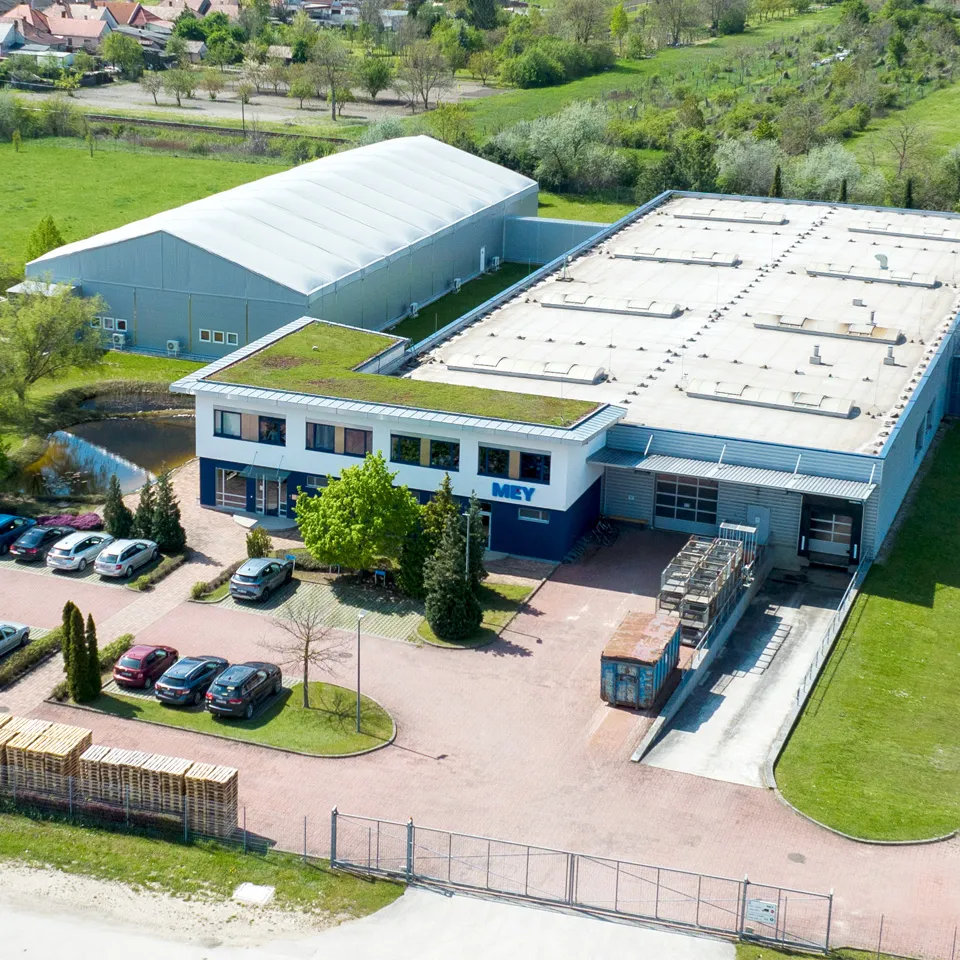
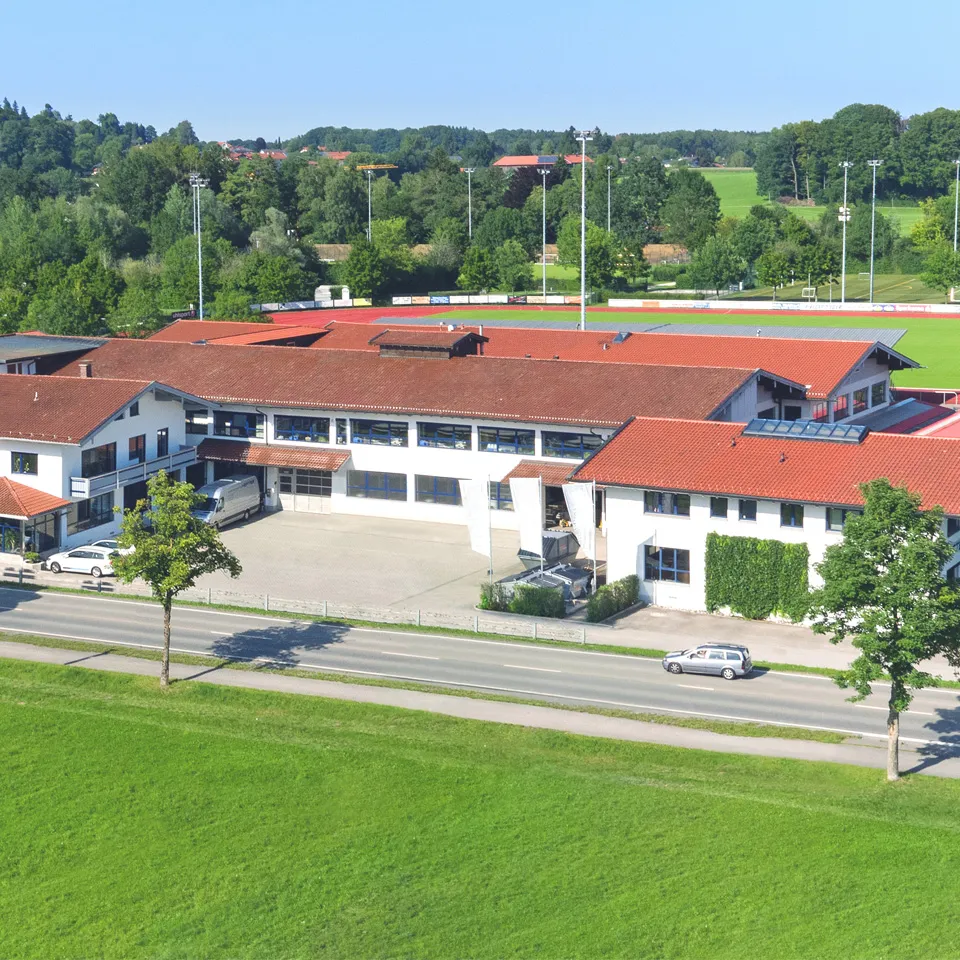
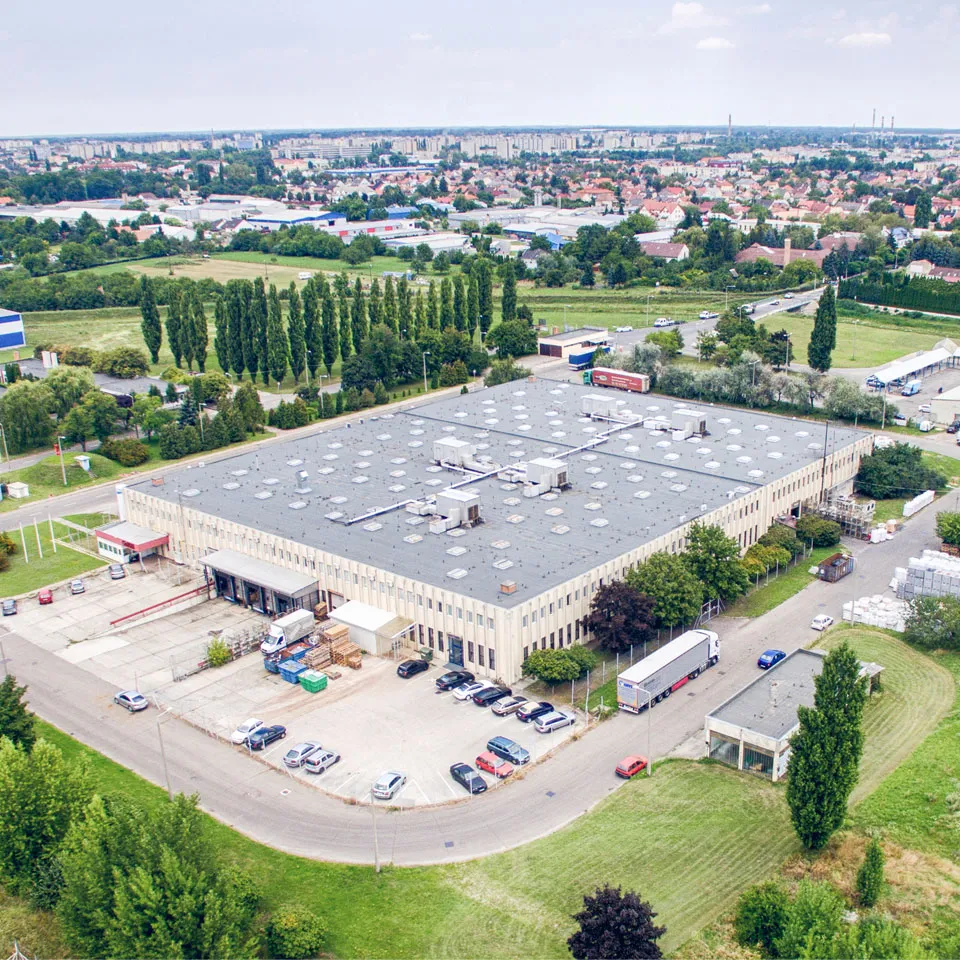
purchasing
- Re-up:
Strategic purchasing in Germany - series:
Operational purchasing in Hungary (series location)
According to the required parts list, the purchased parts are purchased worldwide and sent to the assembly process.
We have the following technologies in-house and are used for the series production of your machines:
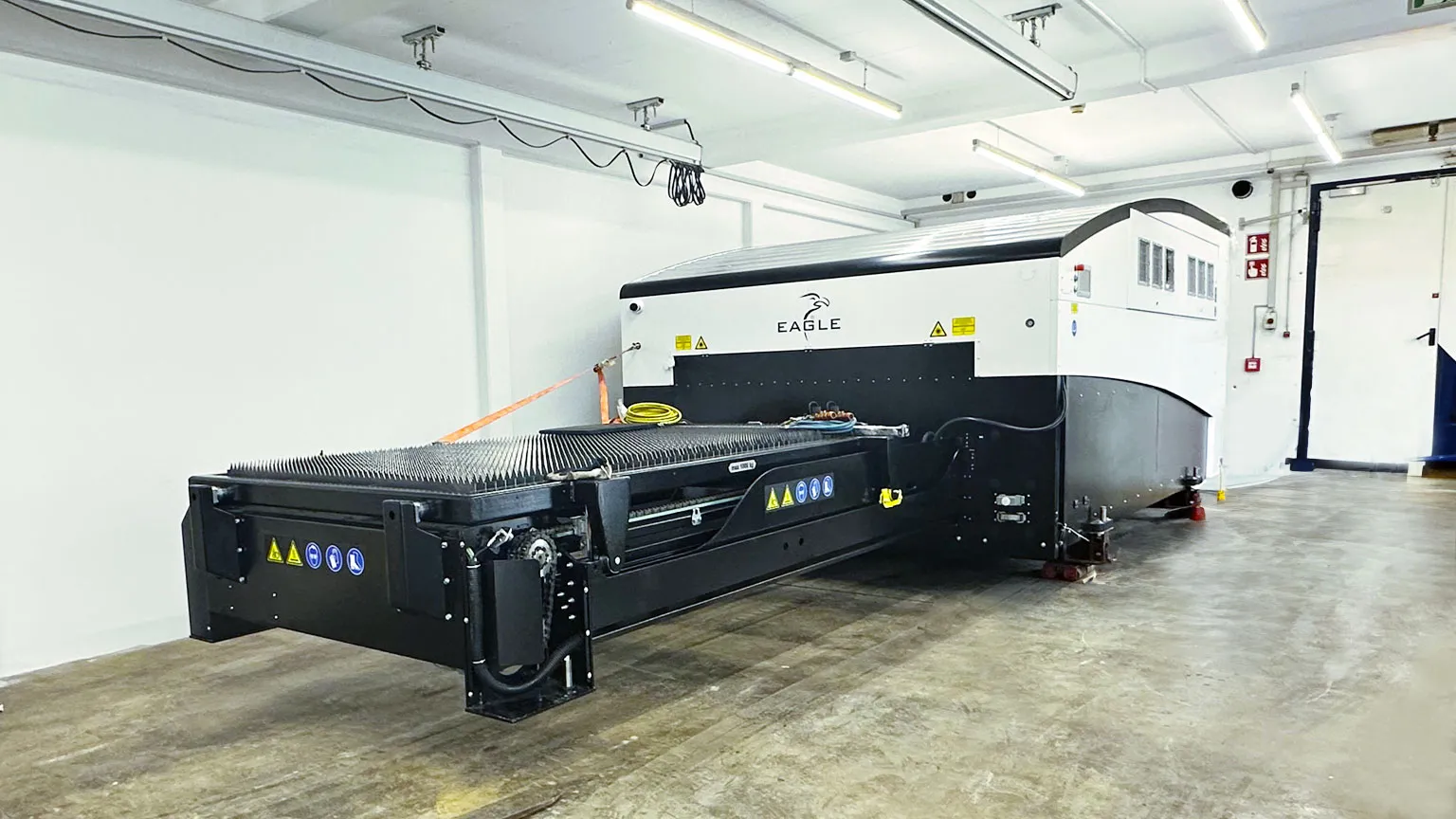
- Punching/laser cutting:
• Max. raw material 3000 x 1500mm
• Max. material thickness: 6mm - Laser cutting:
• Max. raw material 3000 x 1500mm
• Max. material thickness: 12mm steel - Fiber laser cutting:
• Max. raw material 3000 x 1500mm
• Max. material thickness: 60mm steel - VQC board testing
- Grindingmaster:
• Max. passage width 1380mm
• Max. flow height 80mm - LVD ToolCell
With auto. Tool change and angle measurement (3-4 mm)
Of course, we have extensive certificates and the following welding approvals so that your components can be manufactured to the highest standards: DIN 2303 class Q1/Q2 - BK1 to BK4/DIN EN ISO 3834-2
We can offer you the following connection technologies up to welding approval (welding approvals: DIN 2303 class Q1/Q2 - BK1 to BK4):
- Hand welding:
• Max. 3000mm L x 1500mm H x 1500mm W (must be individually tested)
• MIG/MAG/WIG - Robot welding (Yaskawa/Kuka)
• MIG/MAG max. 2000mm L x 1500mm H x 2000mm W (must be individually tested)
• WIG 750x1000x750 (must be individually tested) - Sanding:
To smooth out joints, we grind the welds. This is necessary to achieve the specified optics. - Glue:
We use the gluing of components when sophisticated design and visible surfaces are required. - rivets:
Titgemeyer MS 50 — blind rivet nut up to M8/blind rivets (shaft diameter max. 3mm)
materials
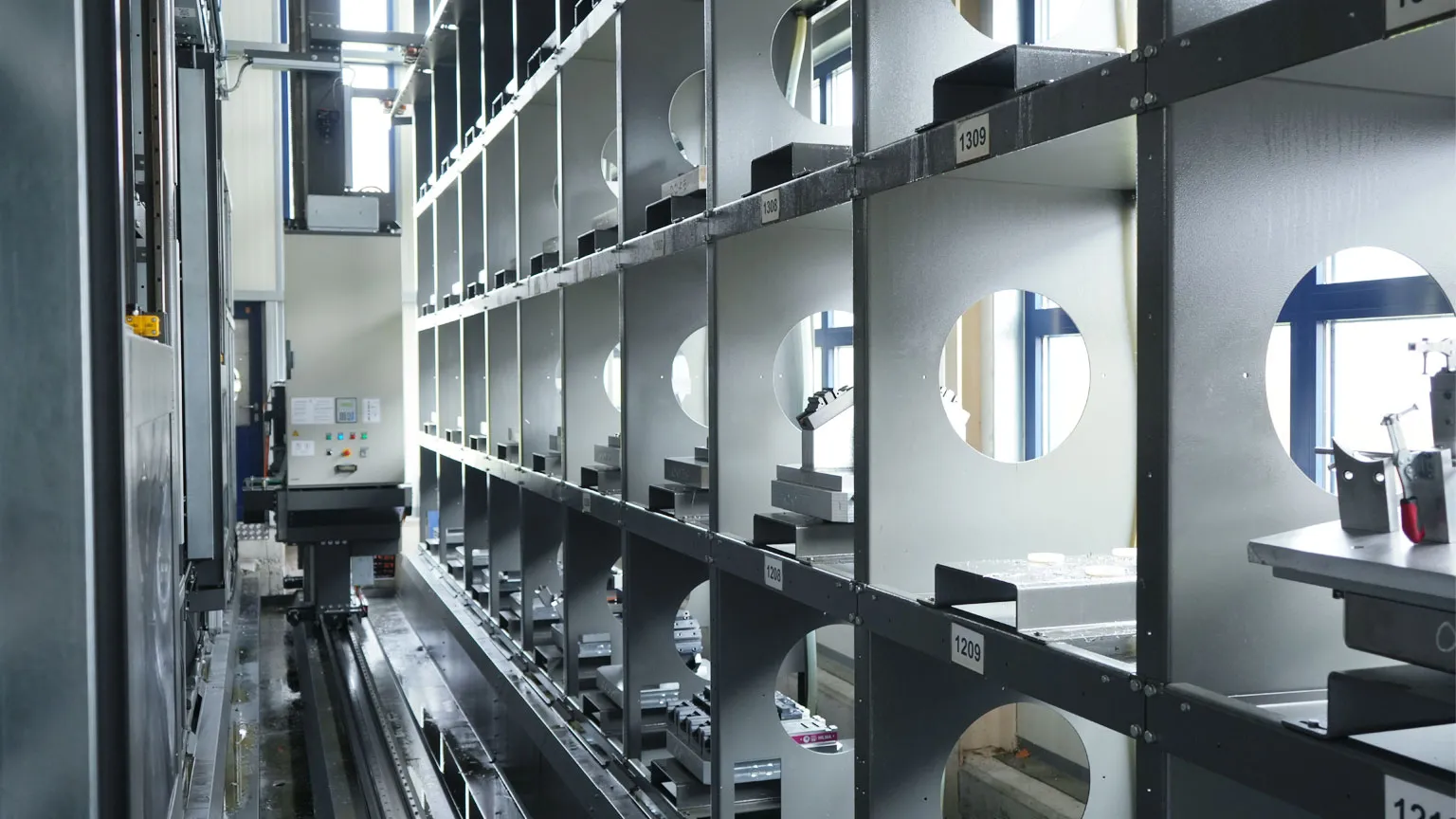
- aluminum
- steel
- stainless steels
- copper
surfaces
- anodizing
- Phosphating & powder coating
- galvanizing
- More surfaces (e.g. gilding) on request
More technologies in use
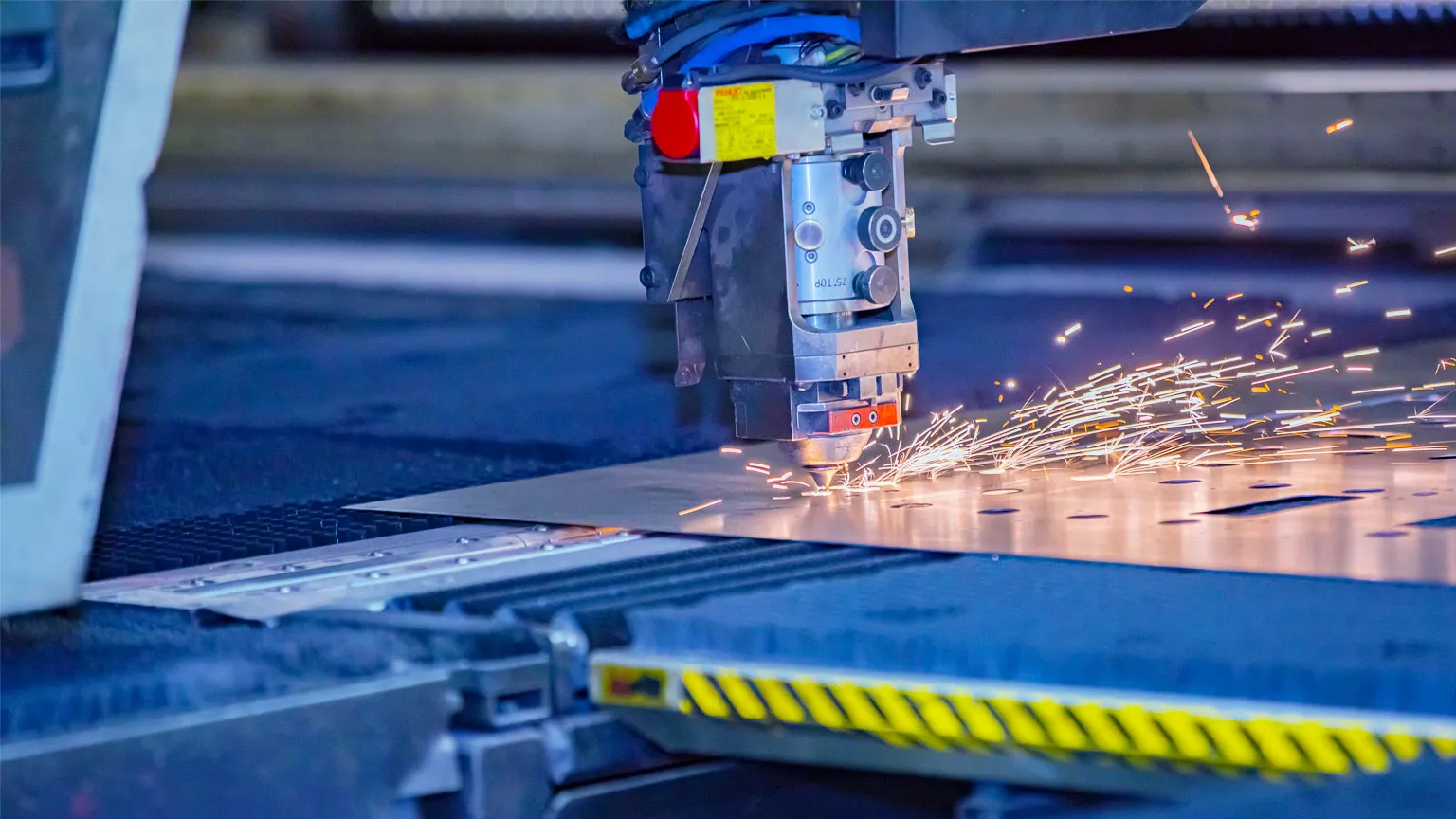
- Fixture construction
- Manual roll bending
- eccentric presses
- High-bay warehouse for metal sheets
- PEM nut setting
- spot welding
Do you have any more questions?
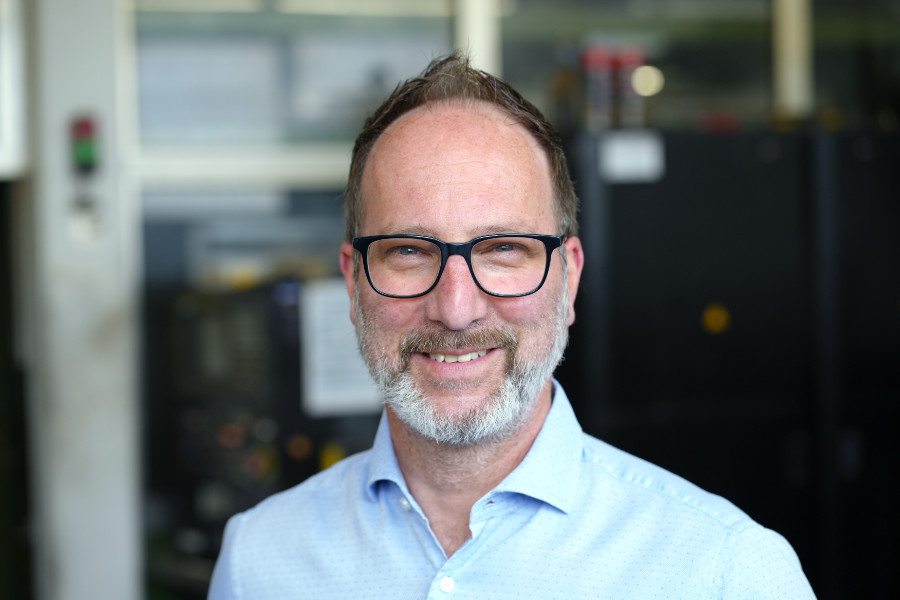
At Mey Maschinenbau Prien, cooperation starts with a personal conversation and, if possible, a personal meeting. We would be happy to show you our production facilities in our main plant in Prien am Chiemsee and our plants in Hungary.
We also assemble ready-to-ship machines including end customer packaging for you.
Here you can find out how we can implement your finished machines.